In 2020... there's an approximately 17 step process to build the average suburban home

Source: https://www.tolerance.org/magazine/fall-2012/struggling-in-suburbia
For as mysterious as the process of building a house may seem from the outside, it's actually a very straight-forward process that has been mastered to proliferate en masse through the suburban neighbourhoods of North America.
-
Apply and receive permits
-
Grading and site preparation
- Clean debris and level lots or dig holes for footers
- Footers have rebar in them so that the concrete wall poured over is better connected. Rebar also will later be connected to the main electrical panel so that in case of lightning, electricity goes to ground
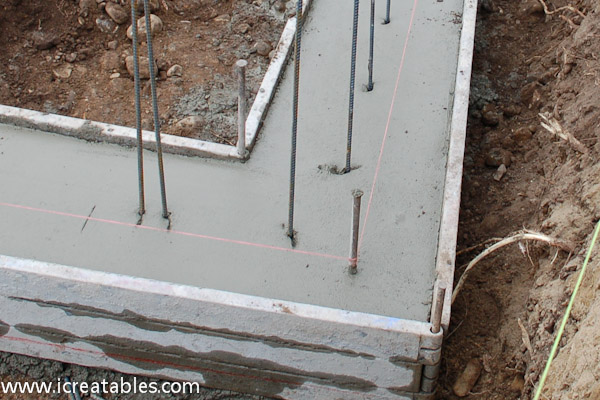
- Footings (structures where the house interfaces with the earth that supports it) are installed
- Areas of the lot are marked for gas, water, electrical, plumbing, etc.
-
Foundation
- Concrete takes up to 4 weeks to cure and is manually smoothed out
- There are underground concrete pillars on concrete footing to avoid sinking house
- Concrete wall poured into forms (which are later removed), more metal bars sticking out to hold 2x4 and earthquake straps
- Foundation can be crawl space, basement, or slab
- Trusses are used to keep the floor from sagging for a basement
- Slabs are less popular in colder climates because the ground freezes
- Crawl spaces keep the house off the ground (important in damp or termite prone areas)
- Spray paint fill line and waterproofing tar where dirt is filled and compacted around foundation
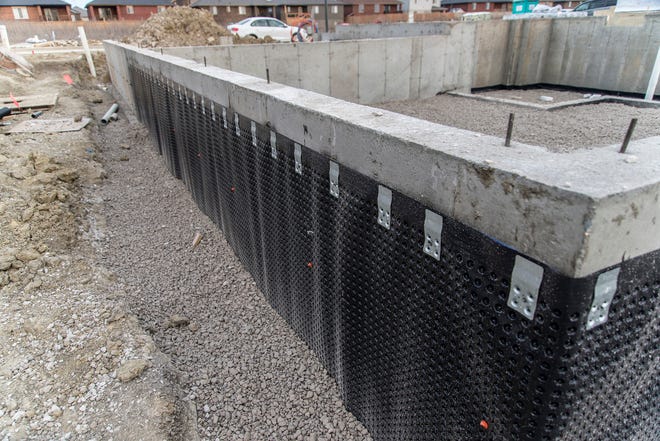
- Gravel is poured before cement to avoid cracking and shifting
- Inspection of foundation by city
-
Framing
- Pressure treated wood is used for anything that touches cement called bottom plate, it's treated and waterproof/rot proof/termite proof
- Build subfloor then frame walls on the ground
- Crossboards used to support house while framing, later removed
- Done by 2x4 or 2x6 (6 is the width, more width means more room for insulation) (i.e. interior walls may use 2x4 while exterior facing are 2x6)
- Holes and headers for windows
- Then cover exterior walls with OSB board, earthquake straps are nailed
- I-beams aka floor joists prevent the floor from sagging
- Main support beams need to be well supported (i.e. by 4 2x4)

-
Roofing
- Trusses then covered with plywood or OSB (oriented strand board - it's waterproof). You can create a roof with or without trusses but trusses are incredibly popular (webbing gives strength)
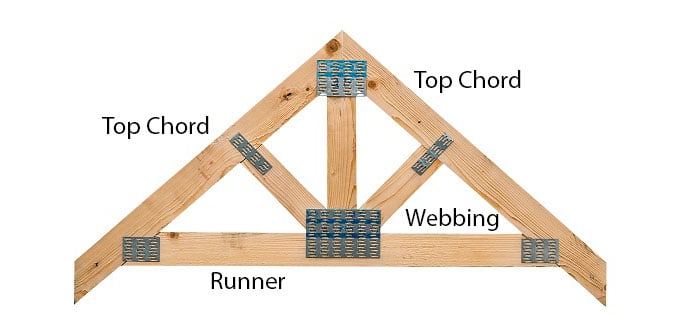
- Ice shield put on first, then building paper (black tar paper or some other material - for waterproofing and wicking using flashing technique) is put on before shingles (which go on quickly and go from bottom to top)
-
Installing windows and doors
- While framing, gaps are supported by header board on top
- Sealed to protect against water penetration
-
Siding
- OSB is first defense against weather, then black paper
- Vinyl siding pieces interlock with eachother
- Finishes such as brick, stone, wood, stucco mamy be used
- After roofing and siding is up, the house is considered “dried in”
-
Electrical
- Place boxes for outlets, switches, then connects from the box (electric panel/main breaker box) to each box and between boxes
-
Plumbing
- Water lines, sewer lines, bathtubs
- Often red is for hot, blue is for cold
- Often white for water, grey for electrical
- Bathtubs and showers are installed early because it's easier to move heavy materials when the house is quite empty
-
HVAC (heating, ventilation, air control) and duct work
- Rough framing, plumbing, and electrical and mechanical systems are inspected for compliance with building codes. Most likely these will be three different inspections
- Duct work connects from furnace to vents in each room

- 4 way inspection - electrical, plumbing, hvac, framing
-
Insulation
- One of the most important qualities of insulation is its thermal performance or R-value, which indicates how well the material resists heat transfer
- The most common types of insulation used in new homes are fiber glass, cellulose and foam. Also may use mineral wool, concrete blocks; foam board or rigid foam, insulating concrete forms (ICFs), sprayed foam, and structural insulated panels (SIPs).

-
Drywall
- Drywall (also called sheet rock - it's super heavy) is a half-inch layer of plaster or gypsum sandwiched between two thick sheets of paper
- Drywall is rot and mold resistant
- Drywall is taped, mudded (joint compound), then sanded. Drywall isn't precisely cut
- Drywall creates a lot of waste from extra material
- Square/round corners done with overlaid pieces with staples, joint compound, sanding
-
Painting and trim (trim is purely decorative around the edges of a room/ windows)
-
Cabinets and counters
- Doors sills, fireplaces, mantles, tile, fixtures, mirrors